Plastic Injection Molding and Mold
Discover the unparalleled accuracy and top-tier quality of our state-of-the-art plastic injection molding technique. Connect with us by submitting your inquiry to unleash the complete capabilities of tailor-made, superior-grade components.
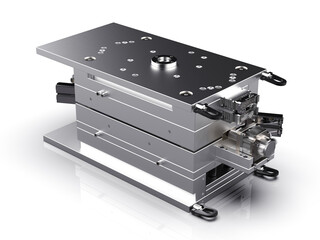
What is Plastic Injection Molding?
Injection molding is the most cost-effective method for mass-producing plastic components. The process involves injecting molten plastic into a mold and then ejecting the solidified part. Plastic injection molding can be used for anything from manufacturing a few prototype parts up to running millions of an identical part. injection molding offers the widest range of materials, colors, cosmetics, polishing, and surface textures.
What is Plastic Injection Molding Used For?
Plastic injection molding offers vast manufacturing potential across diverse industries like consumer electronics, automotive components, medical equipment, tools, toys, and packaging. Various post-processing techniques can be applied to attain specific finishes or textures. It's a cost-effective method for large-scale production of identical or similar plastic parts.
Lingshantech's custom plastic molding service provides on-demand prototyping and production molding solutions. We take a customer-centric approach, which means we manufacture parts in the way you need them, without compromising on design, all at an appropriate price. We offer expert consultations for each injection mold quote and assign project managers to every order, ensuring your parts move seamlessly from design to production. Our team has extensive experience across various industries, particularly in medical injection molding and liquid silicone rubber molding.
What is Molding Cycle Time?
The cycle is the sequence of events that happens during the plastic injection molding process. The cycle begins when the mold closes and the molten plastic polymer is injected into the mold cavity. When the cavity fills, the mold maintains a holding pressure to account for material shrinkage. After that the screw turns, pushing the next shot of molten plastic into place for injection. The mold opens once part has cooled and it is removed from the cavity. The cycle is now complete and will start again.
Why is Molding Cycle Time Important?
Optimizing molding cycle time will save time and money. The faster the cycle time, the more parts that can be produced in a certain time frame. A formula can be used to determine the cycle time of injection molding. The time it takes to make a part using injection molding is calculated as:
Cycle Time = 2M + T + C + E
Where:
(2M) = Mold Open/Close Time x 2
(T) = Injection Time (S/F)
(C) = Cooling Time
(E) = Ejection Time (E)
(S) = Mold Size (in3)
(F) = Flow Rate (in3/min)
The time it takes to open or close the mold and eject the part can last from less than a second up to a few minutes, depending on the size of the mold and machine. The cooling time, which dominates the process, depends on the maximum thickness of the part.
Advantages
Lingshantech’s Advantages of Plastic Injection Molding Technology
High Precision and Complex Geometries: Through precise mold design and advanced injection molding techniques, we can produce plastic parts with high precision and intricate geometries. Whether you require fine details or complex structures, we can meet your requirements.
Low cost and High Efficiency: Plastic injection molding facilitates the simultaneous creation of numerous identical or diverse parts, boosting efficiency. Our advanced equipment and automated processes streamline production cycles, minimizing manual labor for economical manufacturing.
Material Diversity and Customization: We offer a wide range of plastic materials to meet the requirements of various industries and applications. Depending on your project needs, we can select suitable materials and accommodate color adjustments, surface treatments, and special requirements.
High Quality and Reliability: We emphasize rigorous quality control and continuous process monitoring to guarantee the adherence of our plastic parts to stringent quality standards. Through the use of plastic injection molding, we deliver parts that are consistently precise, dimensionally accurate, and dependable.
Cost of Plastic Injection Molding
The cost of plastic injection molding is contingent upon various factors such as the intricacy of the parts, chosen materials, and the volume of production. The primary expenditure lies in the creation of the mold. While simpler molds may incur expenses ranging from $3,000 to $6,000, more intricate molds could cost between $30,000 and $60,000. Production volume also plays a crucial role—the more parts manufactured through injection molding, the lower the per-part cost. Ultimately, the final cost per unit is determined by the type of plastic utilized, the overall mold expense, and the quantity of parts produced. Although initial costs for plastic injection molding might exceed those of other manufacturing methods, the potential savings, with each part costing mere cents when produced in quantities of hundreds, thousands, or millions, can be substantial.
What are the Disadvantages of Injection Molding?
While injection molding boasts numerous advantages, one drawback can be the cost per piece when producing small quantities. At Lingshantech, we have access to diverse manufacturing processes ideal for crafting prototypes or producing low volumes of parts. Get in touch with our experts at Lingshantech to explore alternative manufacturing methods tailored for prototypes or low-volume part runs.
Related Technology
Liangshantech’s Related Technology of Plastic Injection Molding
LingshanTech is a leading company with outstanding technological advantages in the field of plastic injection molding. We combine the latest advanced technologies and innovative solutions to provide customers with high-quality injection molding services. Here are the technological advantages of LingshanTech in the plastic injection molding field:
Advanced Mold Design:
LingshanTech has an experienced engineering team proficient in Computer-Aided Design (CAD) and Computer-Aided Engineering (CAE) technologies. We use advanced simulation analysis during the mold design phase to optimize plastic flow, minimize potential defects, and ensure the accuracy and consistency of part molding.
High-Performance Mold Materials:
To ensure the durability and stability of the molds, LingshanTech adopts high-strength mold materials and state-of-the-art coating technologies. These materials and coatings offer excellent wear resistance and thermal conductivity, ensuring the molds operate reliably in high-volume production environments.
Precision Injection Control:
Our injection production lines are equipped with advanced injection machines and control systems, enabling highly precise injection processes. Precise control of temperature, pressure, and injection speed ensures that each part meets the strict requirements of our customers.
Technological Innovation:
LingshanTech continuously drives technological innovation and closely follows the latest technologies and trends related to plastic injection molding. We maintain a leading position in areas such as micro-injection molding, gas-assisted injection molding, and actively research eco-friendly plastic materials to meet customers' demands for sustainable development.
Smart Manufacturing Applications:
We integrate the concept of Industry 4.0 into our production process, adopting intelligent manufacturing technologies. Through the use of sensors, data analytics, and real-time monitoring, LingshanTech achieves intelligent control and optimization of the production process, enhancing production efficiency and product consistency.
As a leading plastic injection molding company, LingshanTech not only constantly innovates in technology but also strives to provide excellent solutions and high-quality products to our customers. Our professional team will continue to work closely with customers to promote the development and advancement of the industry.
Design Guidelines
Custom Injection Moldings Design Guidelines
Feature | Tip |
Undercuts | Incorporating pass-thru coring helps to minimize undercuts, thereby reducing the complexity and cost of the tool's ejection mechanisms. |
Wall Thickness | Maintaining uniform wall thickness in plastic parts helps prevent wall sink and voids, while thinner walls contribute to shorter cycle times and lower manufacturing costs. |
Drafts | Ensure parts are designed with a minimum draft angle of 0.3°, or up to 5°, for faces with medium textures. |
Ribs/Gussets | Ribs should be 40-60% the thickness of outer walls and should still maintain draft. |
Bosses | To ensure structural integrity, bosses should be designed at 30% of the wall thickness in depth, featuring a 30% edge groove, and attached to side walls or ribs. |
How We Manage Your Injection Molding Project?
Step | Description |
1. Upload Design | Submit your product's 3D design for review by our specialist team. Receive expert insights and recommendations. |
2. Receive Quote | Collaborate with your account manager and technical team to get a detailed quote within 48 hours. |
3. DFM & Tool Approval | Review the Design For Manufacturing (DFM) analysis for your approval before tool construction begins. |
4. Receive T1 Samples | Prior to production, receive a golden sample for approval to ensure it meets your specifications. |
5. Production & Delivery | Parts are manufactured to match the approved sample and promptly delivered to your location. |
6. Reorder as Required | Easily reorder parts by contacting your account manager for any future requirements. |
Material
We’ve worked with many types of resins, including:
Property | Materials |
Impact resistant | ABS, PMMA, PVC, PE, PC |
Wear-resistant | POM, PEEK, UHMW |
Dimensional stability | ABS, PBT, HIPS, PPS |
Chemical resistance | PEEK, PP, PBT, PE, LDPE, PA |
Rubber like | TPU, TPE, Silicone |
Cost-efficient | PP, HDPE, LDPE |
Cosmetic | ABS, PC, HIPS |
Our Custom Service
OUR CUSTOM INJECTION MOLDING SERVICES
Lingshantech specializes in crafting plastic injection molds of diverse complexities, ranging from simple to highly intricate designs. Our custom injection molding services prioritize rapid delivery of prototype and low-volume production components. Leveraging streamlined production processes, we typically provide initial articles in under 13 business days, and expedited projects in as little as five days for simple designs. Our expertise encompasses molds featuring side-pull mechanisms for complex part designs, including overhangs and undercuts. With a broad range of capabilities, we produce parts from 3 mm to 1 m in size, ensuring industry-leading lead times as fast as 20 days. Employing injection machines spanning from 60 to 1300 tons, we accommodate various part complexities, sizes, and volumes, ensuring precision and meeting specific tolerance requirements. Partner with us for superior-quality parts tailored to your needs and punctually delivered.
How Do You Make Plastic Injection Molds?
Injection molds were traditionally built with knee mills, but today, Computer Numerical Control (CNC) machining and Electrical Discharge Machining (EDM) have replaced traditional methods. CNC machining and EDM enable the creation of more intricate molds with precise detailing in less time than conventional machining.
EDM involves using a shaped copper or graphite electrode immersed in paraffin oil, eroding the mold surface through spark erosion in the inverse shape of the electrode. This high-tech method melts material using electricity, achieving levels of detail impossible with traditional milling or grinding methods.
Widely adopted in the mold-making industry, EDM services, like those offered by Lingshantech, produce molds challenging or impossible to machine conventionally. EDM effortlessly handles intricate details like ribs or square corners, difficult for even advanced CNC machining.
However, EDM is limited to electrically conductive materials, allowing shaping of pre-hardened steel molds without requiring subsequent heat treatment. Molds can be made of pre-hardened steel, post-machined heat-treated steel, aluminum, or beryllium-copper alloy, typically chosen based on the number of parts required.
Steel molds offer extended lifespans despite higher initial costs, producing more parts before wearing out. Pre-hardened steel molds have lower wear resistance compared to post-machined heat-treated steel, suitable for lower-volume part requirements.
Multiple-Cavity Molds (Family Molds)
Two-shot injection molding, also known as two-color or dual-material injection molding, refers to the process of injecting two different materials into the same mold to create a single, integrated part. This manufacturing technique allows for the formation of a molded product using two distinct materials, which can differ in color or hardness, enhancing the product's aesthetics and assembly performance.
Multiple-Cavity Molds (Family Molds)
Plastic injection molds have the capability to produce multiple identical parts simultaneously. A mold can be a single-cavity, making one impression per cycle, or a multiple-cavity mold, producing two or more identical parts. Family molds create similar-sized parts in the same quantity, color, and material per cycle, commonly used for components that fit together, such as top and bottom halves of an assembled part. These molds generate corresponding parts each time they open, facilitating the production of assembled components.
Insert molding
Insert Molding, a plastic injection molding technique, integrates metal, ceramic, or plastic components into molten thermoplastic to create sturdy, multi-material parts with enhanced functionalities. For instance, threaded metal rods or nuts can be inserted into parts, facilitating attachment to other components.
This process reduces costs by incorporating secondary parts within the injection molding process rather than adding them post-molding. The resulting insert-molded parts exhibit enhanced durability compared to pieces affixed post-molding. This robustness arises from the insert being encapsulated within the plastic during molding, contrasting with mechanically attached components after molding. Additionally, insert molding decreases the necessity for post-processing labor. However, insert components must endure the high temperatures and pressures inherent in the injection molding process.
Over-molding
Overmolding, a plastic injection molding process, creates multi-material parts often utilized to incorporate handles or grips differing from the main part body. For instance, a power tool may feature a grip made of a softer material than its body. Similarly, game controllers may use various plastics across their bodies.
The process commences with an injection-molded substrate, later inserted into a second mold for the addition of a different material, known as the overmold. Some specialized machines feature multiple injection units enabling overmolding in a single cycle. Two-Shot or Multi-Shot molds produce a single, multi-material part by initially molding a base shape in one material, then injecting a second material into the remaining space.
Overmolding isn't as straightforward as single-material injection molding due to limitations, particularly in material compatibility. Notably, in overmolding, the application of soft materials like TPE (Thermoplastic Elastomer) and LSR (Liquid Silicone Rubber) is crucial. Ensuring compatibility between materials—both chemically and thermally—is essential. Specifically, the substrate material must have a higher melt temperature than the overmolding material to prevent deformation during injection
Large Part Injection Molding
Large part injection molding is a specialized manufacturing process used to produce oversized plastic components and parts. This technique is particularly suitable for creating large and complex parts that are difficult or impossible to produce using traditional molding methods