Advance mould tooling refers to the precision engineering and manufacturing of molds used in producing complex and high-quality components across various industries, such as automotive, electronics, and consumer goods. These molds are crafted using advanced technologies like CNC machining and 3D design to ensure exceptional accuracy and efficiency. Reputable manufacturers specialize in creating durable and reliable tooling solutions, meeting the stringent demands of mass production while minimizing waste and downtime. With cutting-edge materials and innovative techniques, advance mould tooling supports the production of intricate parts with consistent quality and performance.
Basic Information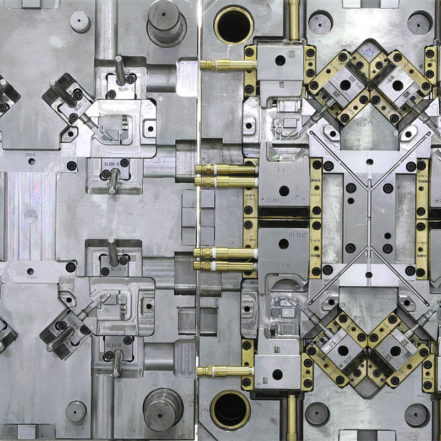
Mold Type: Plastic Injection Mold
Mold Material Options:P20, 718, 738, NAK80, S136
Mold Base Standards: HASCO, DME, MISUMI, JIS, LKM, etc.
Mold Runner System:Cold Runner / Hot Runner
Mold Gate Options:Slide Gate, Sub Gate, Pin-point Gate
Cavity:Single or Multi-Cavity
Design Software Supported:UG, PROE, CAD, SOLIDWORKS
Molding Equipment Used:CNC, Wire Cutting, Milling Machine, EDM
Compatible Raw Materials:ABS, PP, PC, PA6, PA66, PVC, POM, PMMA, PS, etc.
OEM Services:Available—please provide 2D/3D files or samples
Lead Time:Approximately 30 days
One-Stop Service for Tooling
– Initial Consultation: Assess client needs and provide expert advice on design, material selection, and tooling requirements.
– Custom Design: Create tailored designs based on client specifications, utilizing advanced CAD and 3D modeling tools.
– Tooling Fabrication: Manufacture precision molds and tooling using high-quality materials and state-of-the-art machinery.
– Prototype Development: Produce and refine prototypes to validate designs and ensure they meet client expectations.
– Comprehensive Testing: Conduct rigorous testing to verify mold performance, including functionality, durability, and accuracy.
– Surface Finishing: Apply various surface treatments such as polishing, coating, and texturing to achieve desired aesthetics and functionality.
– Production Readiness: Prepare molds for mass production, including final adjustments and quality checks.
– Logistics Management: Handle the complete logistics process, including packaging and shipping to ensure timely and safe delivery.
– Installation Support: Provide guidance and assistance with mold installation and setup to integrate seamlessly into client production lines.
– Quality Assurance: Implement stringent quality control measures throughout the process to ensure all products meet industry standards and client specifications.
– After-Sales Service: Offer ongoing support for maintenance, troubleshooting, and modifications to ensure long-term satisfaction and optimal performance.
Advantages of Our Tooling:
-
Superior Quality:
– Our molds are manufactured using high-grade materials and state-of-the-art techniques, ensuring exceptional durability, precision, and longevity. Each mold undergoes rigorous quality control checks to meet stringent industry standards.
-
Customization:
– We offer highly customizable mold designs tailored to meet specific client requirements. Our team works closely with clients to develop molds that align perfectly with their unique production needs and specifications.
-
Advanced Technology:
– Utilizing the latest in CNC machining, laser cutting, and precision engineering, our molds are crafted with unparalleled accuracy. Our advanced technology ensures consistent, high-quality output and reduces production downtime.
-
Rapid Prototyping:
– We provide quick turnaround times for prototypes, allowing clients to test and validate their designs swiftly. This accelerates the product development process and brings products to market faster.
-
Cost-Effective Solutions:
– By optimizing our production processes and utilizing efficient manufacturing techniques, we offer cost-effective mold solutions without compromising on quality. Our competitive pricing ensures value for money for our clients.
-
Eco-Friendly Materials:
– We prioritize the use of eco-friendly materials and sustainable manufacturing practices. Our commitment to environmental responsibility ensures that our molds have a minimal impact on the environment.