Automotive mould tooling involves the design and production of precision molds used to manufacture automotive parts such as interior components, bumpers, and engine covers. These molds are crafted from high-strength materials like steel or aluminum to ensure durability, dimensional accuracy, and high-volume production efficiency. Custom automotive mould tooling services allow manufacturers to create tailored designs that meet specific vehicle model requirements, ensuring optimal performance, quality, and cost-effectiveness in the automotive industry.
Basic Information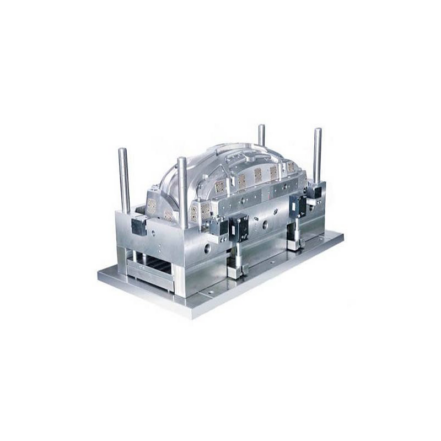
Mold Type: Plastic Injection Mold
Mold Material Options:P20, 718, 738, NAK80, S136
Mold Base Standards: HASCO, DME, MISUMI, JIS, LKM, etc.
Mold Runner System:Cold Runner / Hot Runner
Mold Gate Options:Slide Gate, Sub Gate, Pin-point Gate
Cavity:Single or Multi-Cavity
Design Software Supported:UG, PROE, CAD, SOLIDWORKS
Molding Equipment Used:CNC, Wire Cutting, Milling Machine, EDM
Compatible Raw Materials:ABS, PP, PC, PA6, PA66, PVC, POM, PMMA, PS, etc.
Packaging Method:Wooden pallet or carton
OEM Services:Available—please provide 2D/3D files or samples
Lead Time:Approximately 30 days
One-Stop Service for Tooling
– Initial Consultation: Assess client needs and provide expert advice on design, material selection, and tooling requirements.
– Custom Design: Create tailored designs based on client specifications, utilizing advanced CAD and 3D modeling tools.
– Tooling Fabrication: Manufacture precision molds and tooling using high-quality materials and state-of-the-art machinery.
– Prototype Development: Produce and refine prototypes to validate designs and ensure they meet client expectations.
– Comprehensive Testing: Conduct rigorous testing to verify mold performance, including functionality, durability, and accuracy.
– Surface Finishing: Apply various surface treatments such as polishing, coating, and texturing to achieve desired aesthetics and functionality.
– Production Readiness: Prepare molds for mass production, including final adjustments and quality checks.
– Logistics Management: Handle the complete logistics process, including packaging and shipping to ensure timely and safe delivery.
– Installation Support: Provide guidance and assistance with mold installation and setup to integrate seamlessly into client production lines.
– Quality Assurance: Implement stringent quality control measures throughout the process to ensure all products meet industry standards and client specifications.
– After-Sales Service: Offer ongoing support for maintenance, troubleshooting, and modifications to ensure long-term satisfaction and optimal performance.
Advantages of Our Tooling:
-
Superior Quality:
– Our molds are manufactured using high-grade materials and state-of-the-art techniques, ensuring exceptional durability, precision, and longevity. Each mold undergoes rigorous quality control checks to meet stringent industry standards.
-
Customization:
– We offer highly customizable mold designs tailored to meet specific client requirements. Our team works closely with clients to develop molds that align perfectly with their unique production needs and specifications.
-
Advanced Technology:
– Utilizing the latest in CNC machining, laser cutting, and precision engineering, our molds are crafted with unparalleled accuracy. Our advanced technology ensures consistent, high-quality output and reduces production downtime.
-
Rapid Prototyping:
– We provide quick turnaround times for prototypes, allowing clients to test and validate their designs swiftly. This accelerates the product development process and brings products to market faster.
-
Cost-Effective Solutions:
– By optimizing our production processes and utilizing efficient manufacturing techniques, we offer cost-effective mold solutions without compromising on quality. Our competitive pricing ensures value for money for our clients.