Plastic kitchenware molds are precision-engineered tools used to create a variety of kitchen items, such as measuring cups, spatulas, storage containers, and other utensils. These molds are designed to shape molten plastic into durable, functional, and often aesthetically appealing products. Made from high-quality materials, they ensure consistent quality and high production efficiency in mass manufacturing. By injecting plastic into the mold cavity, manufacturers can quickly produce large quantities of kitchenware items that are lightweight, easy to clean, and versatile for everyday use.
Basic Information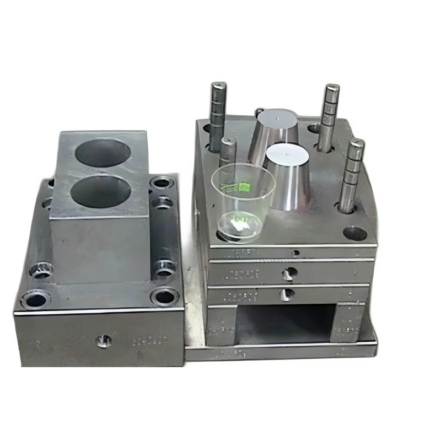
Mold Type: Plastic Injection Mold
Mold Material Options:P20, 718, 738, NAK80, S136
Mold Base Standards: HASCO, DME, MISUMI, JIS, LKM, etc.
Mold Runner System:Cold Runner / Hot Runner
Mold Gate Options:Slide Gate, Sub Gate, Pin-point Gate
Cavity:Single or Multi-Cavity
Design Software Supported:UG, PROE, CAD, SOLIDWORKS
Molding Equipment Used:CNC, Wire Cutting, Milling Machine, EDM
Compatible Raw Materials:ABS, PP, PC, PA6, PA66, PVC, POM, PMMA, PS, etc.
Packaging Method:Wooden pallet or carton
OEM Services:Available—please provide 2D/3D files or samples
Lead Time:Approximately 30 days
Customization Service for Molds
– Design Consultation:Collaborate with clients to understand specific design requirements and preferences.
– Technical Drawings:Create detailed technical drawings and specifications based on client input.
– Material Selection:Assist in choosing appropriate materials for both the mold and the final product to ensure optimal performance.
– Tooling Development:Develop custom tooling and molds tailored to meet precise specifications and production needs.
– Prototype Production:Produce prototypes to validate design, functionality, and material choices before full-scale production.
– Mold Fabrication:Utilize advanced manufacturing techniques to create high-quality, durable molds.
– Surface Finishing:Apply various surface treatments, including polishing, coating, and texturing, to meet aesthetic and functional requirements.
– Testing and Validation:Conduct rigorous testing of molds to ensure they meet quality standards and performance expectations.
– Adjustments and Iterations: Make necessary adjustments and refinements based on prototype testing and client feedback.
– Production Support:Provide ongoing support throughout the production process, including troubleshooting and maintenance.
– Quality Assurance: Implement stringent quality control measures to ensure the molds meet industry standards and client specifications.
– Delivery and Installation:Manage logistics for timely delivery and offer installation support to ensure seamless integration into the production line.
Quality Documentation
- ISO 9001:2015 Certification
- IATF 16949 Certification
- First Article Inspection (FAl)
- PPAP Report(Production Part Approval Process)
- Material Technical Data Sheets (TDS)
- CMM Inspection Report
- SPC Report (Statistica Process Control)
- Material Certificates
- Dimensional Inspection Report (CMM)
- DFM feedback