Leaking basket mould tools are specialized molds designed for producing plastic baskets with drainage holes or perforations, typically used in applications where liquid flow or air circulation is required, such as in agricultural, food storage, or industrial environments. These molds are precisely engineered to create baskets with consistent hole patterns that ensure proper drainage while maintaining structural integrity. Made from durable materials capable of withstanding the stresses of injection or blow molding processes, leaking basket mould tools are built for high efficiency and long service life, allowing for the mass production of reliable, leak-proof baskets with optimal functionality.
Basic Information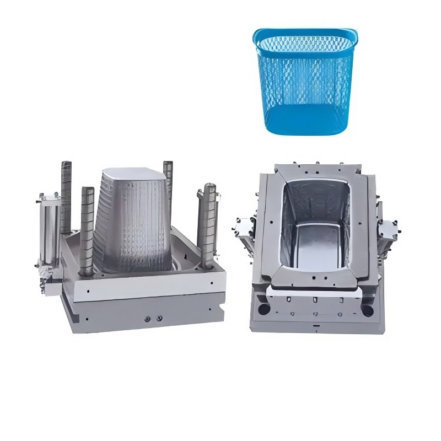
Mold Type: Plastic Injection Mold
Mold Material Options:P20, 718, 738, NAK80, S136
Mold Base Standards: HASCO, DME, MISUMI, JIS, LKM, etc.
Mold Runner System:Cold Runner / Hot Runner
Mold Gate Options:Slide Gate, Sub Gate, Pin-point Gate
Cavity:Single or Multi-Cavity
Design Software Supported:UG, PROE, CAD, SOLIDWORKS
Molding Equipment Used:CNC, Wire Cutting, Milling Machine, EDM
Compatible Raw Materials:ABS, PP, PC, PA6, PA66, PVC, POM, PMMA, PS, etc.
Packaging Method:Wooden pallet or carton
OEM Services:Available—please provide 2D/3D files or samples
Lead Time:Approximately 30 days
Why Choose Us?
-
Multi-Language Capability:
– Our team is proficient in multiple languages, ensuring seamless communication with clients from diverse linguistic backgrounds. This capability allows us to effectively understand and meet your specific needs, regardless of your location.
-
On-Site Material Inspection:
– We conduct thorough on-site inspections of all materials before they are used in production. This rigorous process ensures that only the highest quality materials are utilized, maintaining the integrity and durability of the final product.
-
Design-Based Customization:
– We offer extensive customization based on your design requirements. Our experienced engineers collaborate closely with you to develop molds that precisely match your specifications, ensuring optimal performance and functionality.
-
Finished Product Inspection:
– Each finished product undergoes a comprehensive inspection to verify it meets all quality standards and customer specifications. This meticulous approach guarantees that you receive products of the highest quality and reliability.
-
Sample-Based Customization:
– We provide customization based on sample submissions. This process allows us to replicate and enhance existing designs, ensuring the final product aligns perfectly with your expectations.
-
Full Customization:
– We offer full customization services, tailoring every aspect of the mold to your specific needs. From design to production, we ensure that every detail is customized to meet your unique requirements.
Quality Control
Ensuring product quality is paramount throughout the entire manufacturing process. Before mass production, we always create a pre-production sample to verify that the mold meets the exact specifications and functionality required by the client. This stage involves dimensional accuracy checks using CMM (Coordinate Measuring Machine) for precise measurements, calipers for detailed part dimensions, and surface roughness testers to evaluate the finish. Material verification is conducted using spectrometers to ensure the correct metal composition.
Before shipment, a final inspection is conducted using hardness testers to confirm proper mold hardness and wear resistance, and injection molding machines to test mold performance under real production conditions. We also employ visual inspection tools and microscopes to detect surface defects such as flash, warping, or other imperfections. Additionally, pressure and temperature sensors are used to verify the mold’s capability to handle production stress. Only after these rigorous tests are passed do we authorize the mold for shipping, ensuring that the customer receives a precision-engineered tool, fully ready for high-quality production.