Our plastic injection molding molds for instruments and apparatus are designed with precision and adaptability to meet the specific needs of each client. Our factory is equipped with advanced injection molding technology, allowing us to deliver highly accurate, durable molds that ensure optimal performance for your instruments and apparatus. We specialize in custom mold design and manufacturing, offering rapid prototyping to quickly refine and perfect your designs. With our extensive manufacturing capabilities, we guarantee high-quality production, reliable delivery, and competitive pricing, positioning us as a trusted partner for your custom molding needs.
Basic Information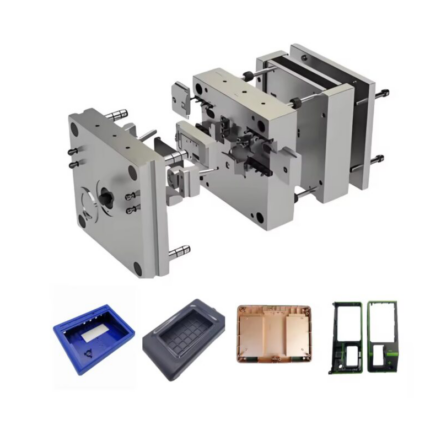
Place of Origin:Xiamen, China
Product Material: Steel
Plastic Material :PP, PC, PA, PA6, ABS, PET, PVC, POM, etc.
Gate System :Cold Runner / Hot Runner
Ejection System: Pin / Stripper Plate, etc.
A.B Plate Material: 1.1730 / P20, etc.
Tool Life: Prototype to 1,000,000 shots
Cavity & Core Material :P20 / H13 / NAK80 / S50C / S136 / 738H, etc.
Surface Finish :Polish / Texture / Heat Treatment, etc.
Cavities: Single / Multiple / Family Mold
Lead Time: 3 to 8 weeks
Customization Service for Molds
– Design Consultation:Collaborate with clients to understand specific design requirements and preferences.
– Technical Drawings:Create detailed technical drawings and specifications based on client input.
– Material Selection:Assist in choosing appropriate materials for both the mold and the final product to ensure optimal performance.
– Tooling Development:Develop custom tooling and molds tailored to meet precise specifications and production needs.
– Prototype Production:Produce prototypes to validate design, functionality, and material choices before full-scale production.
– Mold Fabrication:Utilize advanced manufacturing techniques to create high-quality, durable molds.
– Surface Finishing:Apply various surface treatments, including polishing, coating, and texturing, to meet aesthetic and functional requirements.
– Testing and Validation:Conduct rigorous testing of molds to ensure they meet quality standards and performance expectations.
– Adjustments and Iterations: Make necessary adjustments and refinements based on prototype testing and client feedback.
– Production Support:Provide ongoing support throughout the production process, including troubleshooting and maintenance.
– Quality Assurance: Implement stringent quality control measures to ensure the molds meet industry standards and client specifications.
– Delivery and Installation:Manage logistics for timely delivery and offer installation support to ensure seamless integration into the production line.