Overview
Plastic Plates and Cups Molds are precision-engineered tools used in the manufacturing of disposable plastic plates and cups. These molds are designed to produce high-quality, consistent products in various shapes, sizes, and designs, suitable for foodservice, catering, and packaging industries. Made from durable materials, plastic molds ensure efficient production with minimal defects, allowing for high-volume output while maintaining product integrity. The molds are designed for ease of use in injection molding or thermoforming processes, delivering cost-effective solutions for creating lightweight, sturdy, and environmentally responsible plastic plates and cups.
Basic Information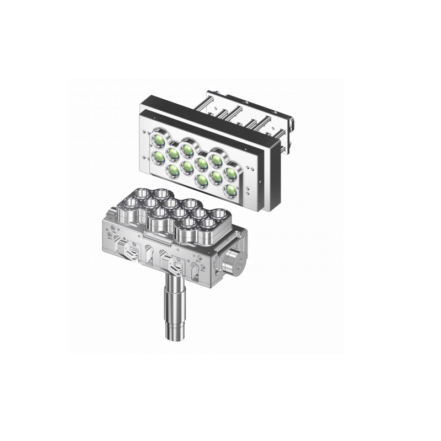
Mold Type: Plastic Injection Mold
Mold Material Options:P20, 718, 738, NAK80, S136
Mold Base Standards: HASCO, DME, MISUMI, JIS, LKM, etc.
Mold Runner System:Cold Runner / Hot Runner
Mold Gate Options:Slide Gate, Sub Gate, Pin-point Gate
Cavity:Single or Multi-Cavity
Design Software Supported:UG, PROE, CAD, SOLIDWORKS
Molding Equipment Used:CNC, Wire Cutting, Milling Machine, EDM
Compatible Raw Materials:ABS, PP, PC, PA6, PA66, PVC, POM, PMMA, PS, etc.
Packaging Method:Wooden pallet or carton
OEM Services:Available—please provide 2D/3D files or samples
Lead Time:Approximately 30 days
Customization Service for Molds
– Design Consultation:Collaborate with clients to understand specific design requirements and preferences.
– Technical Drawings:Create detailed technical drawings and specifications based on client input.
– Material Selection:Assist in choosing appropriate materials for both the mold and the final product to ensure optimal performance.
– Tooling Development:Develop custom tooling and molds tailored to meet precise specifications and production needs.
– Prototype Production:Produce prototypes to validate design, functionality, and material choices before full-scale production.
– Mold Fabrication:Utilize advanced manufacturing techniques to create high-quality, durable molds.
– Surface Finishing:Apply various surface treatments, including polishing, coating, and texturing, to meet aesthetic and functional requirements.
– Testing and Validation:Conduct rigorous testing of molds to ensure they meet quality standards and performance expectations.
– Adjustments and Iterations: Make necessary adjustments and refinements based on prototype testing and client feedback.
– Production Support:Provide ongoing support throughout the production process, including troubleshooting and maintenance.
– Quality Assurance: Implement stringent quality control measures to ensure the molds meet industry standards and client specifications.
– Delivery and Installation:Manage logistics for timely delivery and offer installation support to ensure seamless integration into the production line.
Advantages of Our Mold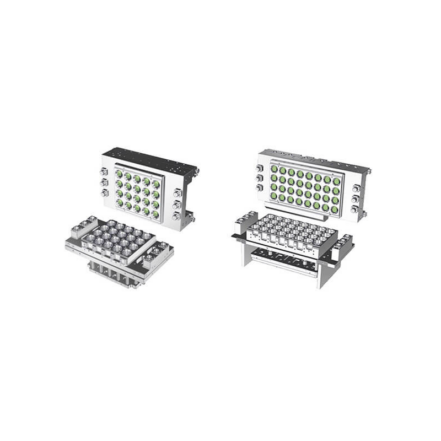
-
Superior Quality:
– Our molds are manufactured using high-grade materials and state-of-the-art techniques, ensuring exceptional durability, precision, and longevity. Each mold undergoes rigorous quality control checks to meet stringent industry standards.
-
Customization:
– We offer highly customizable mold designs tailored to meet specific client requirements. Our team works closely with clients to develop molds that align perfectly with their unique production needs and specifications.
-
Advanced Technology:
– Utilizing the latest in CNC machining, laser cutting, and precision engineering, our molds are crafted with unparalleled accuracy. Our advanced technology ensures consistent, high-quality output and reduces production downtime.
-
Rapid Prototyping:
– We provide quick turnaround times for prototypes, allowing clients to test and validate their designs swiftly. This accelerates the product development process and brings products to market faster.
Surface Treatment
-
Polishing:
This process refines the mold’s surface finish, reducing friction and improving both appearance and performance. A well-polished mold leads to high-quality, defect-free products with superior surface smoothness.
-
Texturing:
Texturing involves applying intricate patterns or designs to the mold surface. It’s ideal for creating unique finishes on the final product, such as leather-like textures or fine grooves, enhancing both functionality and visual appeal.
-
Hard Chrome Plating:
Hard chrome plating enhances the hardness and wear resistance of the mold. It’s particularly effective for molds subjected to high friction, ensuring prolonged tool life and consistent product quality.
-
Nitriding:
Nitriding diffuses nitrogen into the steel surface of the mold, forming a hard, wear-resistant layer. This treatment is essential for molds used in high-stress applications, enhancing their durability and performance.
-
Titanium Nitride (TiN) Coating:
TiN coating provides a gold-colored, hard surface that enhances wear resistance, reduces friction, and improves mold release properties, making it ideal for high-volume production runs.
-
Nickel Plating:
Nickel plating offers excellent corrosion resistance, protecting the mold from chemical or environmental exposure, particularly useful for molds operating in harsh conditions.
-
Electroless Nickel Plating:
This uniform coating provides enhanced hardness, wear resistance, and corrosion protection without the need for an electric current. It ensures long-lasting mold performance, even in challenging environments.
-
Anodizing:
Commonly used for aluminum molds, anodizing provides a durable, corrosion-resistant surface, allowing for color customization and enhanced aesthetic quality for easy identification.
-
Black Oxide Coating:
Black oxide coating improves the mold’s corrosion resistance and appearance by creating a uniform black finish. It also reduces light reflection, beneficial for certain production environments.
-
PVD (Physical Vapor Deposition) Coating:
PVD applies thin, durable layers of materials such as titanium, chromium, or zirconium to the mold surface, significantly increasing wear resistance, reducing friction, and improving mold longevity.
-
Matt Finish:
A matt finish reduces surface gloss, creating a non-reflective surface ideal for products requiring a subdued, textured look. This finish can enhance the overall appearance and tactile quality of the molded part.
-
VDI (Verein Deutscher Ingenieure) Textures:
VDI textures are standardized surface finishes commonly used in plastic injection molding. These textures range from fine to coarse and are essential for creating desired finishes on the final product.
-
SPI (Society of the Plastics Industry) Finishes:
SPI surface finishes are industry-standard grades for plastic injection molds, ranging from mirror-like finishes to rough textures. Each grade offers distinct advantages based on the application and product requirements.
-
Ball Burnishing:
Ball burnishing is a surface treatment that involves the mechanical smoothing of the mold surface through the application of steel balls under pressure. This process increases the surface hardness, enhances corrosion resistance, and provides a highly polished, defect-free finish.